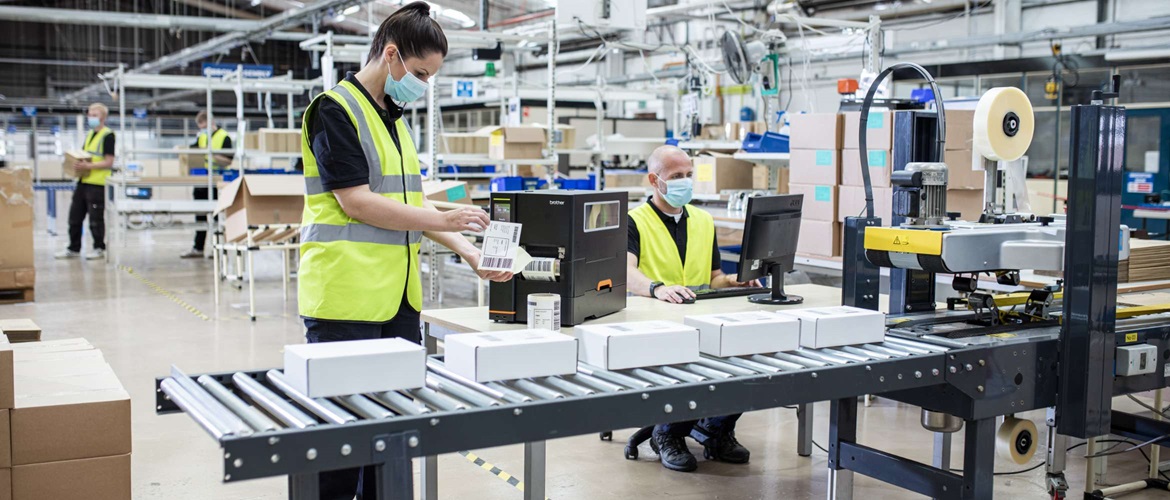
Comment assurer l’exactitude de l’étiquetage?
La précision et la lisibilité des étiquettes à codes barres sont essentielles aux opérations de fabrication et de logistique d’aujourd’hui, qui s’étendent à l’échelle mondiale.
Les entreprises veulent s’assurer que les étiquettes à codes barres imprimées sur site sont conformes aux normes du client et de l’industrie et qu’elles sont lisibles tout au long de la chaîne d’approvisionnement. Elles ne veulent plus limiter les contrôles de lecture à un certain nombre de codes barres dans un lot.
Bien que la plupart des événements de vérification actuels se fassent avec des codes barres 1D, le passage aux codes 2D renforcera l’intérêt pour ce type de fonctionnalité. En effet, les concepteurs d’étiquettes et les imprimantes d’étiquettes/étiqueteuses seront désormais en mesure d’intégrer davantage d’informations dans un espace limité, réduisant ainsi la taille des champs tout en conservant la lisibilité.
Des étiquettes lisibles garantissent la traçabilité de bout en bout, améliorant ainsi les opérations de la chaîne d’approvisionnement et l’efficacité globale. Les solutions de contrôle de l’étiquetage par validation et vérification des données utilisent des équipements de lecture à caméra ou basés sur la vision et exigent une cohérence avec les bases de données et les équipements d’étiquetage. Les vérificateurs déclenchent un signal lorsqu’ils rencontrent une étiquette mal imprimée ou incorrecte, avec la possibilité éventuelle d’interrompre la production pour permettre aux utilisateurs de déterminer et de corriger la cause de l’erreur, et également de prendre des mesures pour isoler le ou les produits douteux de la ligne.
Pourquoi les entreprises font-elles de plus en plus attention à la validation et à la vérification?
VDC Research, qui fait autorité sur les marchés mondiaux des technologies d’identification et de capture de données automatiques (AIDC), a récemment sondé les entreprises afin de mieux comprendre les investissements technologiques en matière de capture de données et d’étiquetage.
L’objectif ultime est de réduire les risques associés aux erreurs d’étiquetage tout en améliorant la précision globale. Les entreprises interrogées ont indiqué évaluer de plus en plus l’achat de systèmes d’inspection, de validation et de vérification afin de réduire, voire d’éliminer complètement, l’incidence des erreurs. L’intégration de la validation et de la vérification des codes barres comme partie intégrante du processus d’impression des étiquettes aide les entreprises à vérifier l’exactitude et la qualité afin de renforcer leurs efforts en matière de traçabilité.
VDC estime que, sans vérification, les codes barres erronés ne sont probablement pas identifiés tant qu’ils ne sont pas illisibles. Presque toutes les entreprises interrogées (96 %) ont indiqué avoir réalisé ou prévu des investissements dans des solutions d’inspection qui confirment la qualité des données, des caractères et des nombres sur les étiquettes et qui identifient les étiquettes qui ne sont pas conformes à la réglementation et aux exigences des clients.
Certaines recommandations non contraignantes incluent le respect des normes ISO/CEI telles que la 15416 (spécifications pour essai de qualité d’impression des codes à barres - symboles linéaires), la 15415 (spécifications pour essai de qualité d’impression des codes à barres - symboles bidimensionnels) et la 29158 (ligne directrice de qualité du marquage direct sur pièce).
Les entreprises envisagent et investissent dans des technologies qui les aideront à réduire les risques associés aux erreurs d’étiquetage et à l’expédition de produits dotés d’étiquettes mal imprimées et illisibles. Ce type d’achat aura un impact positif sur leurs fonctions de fabrication et de distribution et se traduira par une baisse des rappels et une hausse de la satisfaction client.

Qu’est-ce qui motive les investissements dans les systèmes de vérification et de validation des étiquettes?
Voici les principaux facteurs qui contribuent à la hausse de la demande et de l’intérêt pour ces systèmes d’inspection:
- La nécessité d’améliorer l’efficacité opérationnelle globale est plus forte que jamais. Les entreprises peinent à quantifier les coûts réels associés aux erreurs d’étiquetage. Cependant, elles font un effort concerté pour réduire l’incidence globale des erreurs et augmenter la productivité. La volonté de standardiser les investissements dans les technologies d’étiquetage est un pas dans cette direction. L’automatisation des processus liés à l’impression d’étiquettes peut garantir la cohérence et la conformité aux normes réglementaires, car il n’y a pas de place pour les erreurs de saisie manuelle des données. Les solutions d’inspection basées sur la vision s’invitent désormais dans le débat, car elles permettent de standardiser le processus d’impression des étiquettes, quel que soit le lieu.
- Des contrôles de qualité stricts sont désormais essentiels pour limiter les perturbations de la production et de la livraison. Il est de plus en plus nécessaire d’accéder aux données variables et de les imprimer pour les applications d’étiquetage, en particulier dans les environnements à volume élevé avec des exigences complexes. L’étude de VDC montre qu’un grand volume d’étiquettes imprimées pour des applications d’emballage, de réapprovisionnement et d’expédition exige des informations variables précises. La nécessité d’évaluer la qualité des étiquettes sur les produits avant qu’ils ne quittent la production est plus importante que jamais. La validation et la vérification en temps réel permettront de répondre à cette exigence spécifique de vérification de la qualité des données afin de soutenir les entreprises dans leur objectif de traçabilité de bout en bout. Les solutions d’inspection des étiquettes offrent plusieurs niveaux de vérification afin de garantir que les étiquettes ont été correctement appliquées sur les produits, qu’elles correspondent au contenu à imprimer et qu’elles sont lisibles (en détectant les têtes d’impression défectueuses avant qu’elles n’entraînent une interruption de service imprévue).
- Les incohérences dues aux erreurs d’étiquetage sont inacceptables dans le monde d’aujourd’hui où tout va très vite. Aujourd’hui, les entreprises sont de plus en plus mondialisées, tant du point de vue de l’approvisionnement que de la distribution. Il est devenu important d’être non seulement agile et flexible dans son mode de fonctionnement, mais aussi de repenser les stratégies d’investissement et de mise en œuvre des technologies afin d’éliminer les incohérences dans les processus. La nécessité d’un étiquetage précis et d’une visibilité en temps réel du mouvement des marchandises n’a jamais été aussi grande, même si les coûts sont scrutés au plus près. L’ajout de fonctionnalités d’inspection visuelle automatique sera apprécié pour réduire l’incidence des erreurs et, par conséquent, améliorer la productivité globale.
- Les exigences de conformité changent constamment, ce qui modifie les exigences en matière d’automatisation des processus. Les principaux organismes de réglementation internationaux et les entreprises clientes recommandent à leurs partenaires d’inspecter suffisamment la qualité des codes barres. Le but est de renforcer la traçabilité des pièces automobiles, des dispositifs médicaux, des produits pharmaceutiques, etc. Par exemple, la FDA américaine a publié dans son projet de directives sur l’UDI que « si une étiqueteuse choisit une forme de code barres de l’AIDC, la qualité d’impression de la forme de code barres de l’UDI doit être testée ».
L’étude principale de VDC montre que les organisations peuvent avoir des processus en place qui exigent la conformité aux normes ANSI, avec une note globale de C ou supérieure. La recommandation relative à la qualité de l’étiquetage doit être harmonisée entre les secteurs et les catégories de produits, en particulier quand l’échelle des opérations et les réglementations transfrontalières entrent en jeu.
- L’automatisation des impressions permet de retirer de l’équation les erreurs de saisie manuelle des données. Tout problème de lisibilité peut avoir des implications financières importantes pour les fabricants ainsi que pour leurs réseaux de fournisseurs et de distributeurs. L’étude de VDC montre que parmi les coûts quantifiables liés aux erreurs d’étiquetage des codes barres, les principaux sont les rappels coûteux (34 %), les déchets générés par le réusinage et la mise au rebut (26 %) et les rétrofacturations (23 %). L’automatisation des impressions figure en tête de liste des priorités d’investissement des entreprises, le but étant que le facteur humain n’intervienne plus dans le processus de création d’étiquettes. L’ajout de fonctionnalités d’inspection visuelle automatisée, avec AutoID et du matériel de vision, aidera les entreprises à annuler les étiquettes illisibles et à automatiser la réimpression requise en cas de codes barres illisibles.
Comment les entreprises contrôleront-elles la qualité de l’étiquetage à l’aide de ces solutions?
L’étude de VDC montre que le taux d’erreur d’étiquetage est légèrement supérieur à 3 %. Ces erreurs sont généralement dues à des facteurs tels que des processus d’étiquetage incohérents dans des lieux éparpillés et la vérification manuelle de jeux d’étiquettes à code barres spécifiques dans des lots désignés. Les fonctions d’inspection des étiquettes contribuent à faire progresser les produits dans la chaîne d’approvisionnement proposée sans interruption inutile, ce qui permet aux entreprises de réduire les risques opérationnels globaux.
L’objectif ultime est de rendre le processus d’impression exempt d’erreurs. La validation et la vérification des données d’étiquetage en cours de fabrication contribueront à atteindre cet objectif et permettront aux entreprises de scanner, de vérifier, d’évaluer et éventuellement d’enregistrer chaque étiquette imprimée. L’automatisation de l’impression des étiquettes sera essentielle pour atteindre cet objectif. VDC estime qu’il sera difficile de répondre manuellement aux exigences de mise à jour et de validation des modèles individuels si les entreprises ne tirent pas parti des capacités des processus d’étiquetage dynamique.
L’adoption croissante des codes barres 2D riches en données fera mieux connaître les solutions de validation et de vérification des étiquettes et accroîtra les investissements dans ce domaine.
Cette évolution est inéluctable, car ces codes barres continuent de démontrer leur capacité à intégrer davantage de données dans moins d’espace, ainsi que la souplesse offerte par les vérificateurs 2D dans la lecture et la vérification des erreurs. Les applications telles que la traçabilité des pièces automobiles, la représentation précise des exigences de sérialisation/UDI dans les sciences de la vie et l’adoption croissante des codes 2D dans l’industrie agroalimentaire seront en pointe.
Cliquez ici pour en savoir plus sur les solutions Brother pour le transport et la logistique.